Cleaners for stone grinding mills.
Effective cleaning cancels the risk of producing food which is not hygienically safe.
Cleaning must be carried out with the greatest care, to free the outside of every grain of harmful waste including mycotoxins, bacteria, dirt or other impurities.
Even in the case of organic grain.
This passage is particularly important for whole grain products, since these foods also contain the external part of the grain, or the bran, the “barrier” which protects the inner seed from external impurities.
Biostonemill can offer you cleaning machines to assure you that the grain you grind with your stone mill is clean, to produce hygienically safe, healthy flour.
BioStoneMill Cleaners. The cleaner the grain, the safer your business.


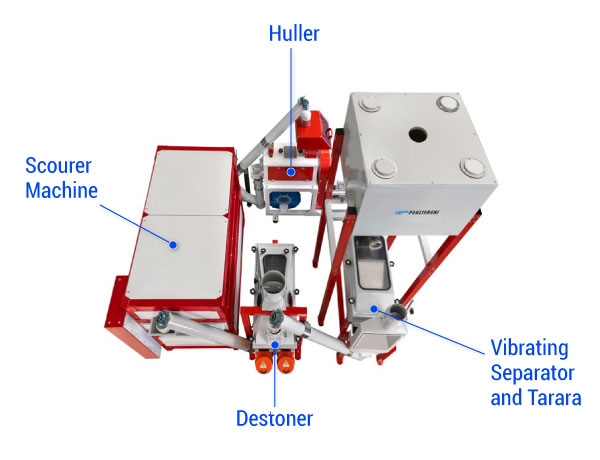
FLOWMETER
Device measuring the quantity of cereal or legumes, at the entry.
VIBRATING SEPARATOR AND TARARA
Vibrating separator with tarara: consists of two overlapping vibrating sieves that allow to eliminate the different sized impurities from the cereal.
The upper sieve separates impurities bigger than the cereal, while the lower sieve separates shriveled kernels, soil and all impurities smaller than the cereal.
The choice of the sieve holes opening therefore depends on the size and shape of the cereal being treated.
The sieved cereal passes through the tarara airflow that eliminates shriveled kernels and hay that are lighter than the treated cereal.
In case of processing more than one cereal, it is possible to have more sieves in stock, each of which is suitable for a type of cereal.
The screens are vibrated by two motion-vibrators.
DESTONER
The main purpose of this machine is the stone elimination which, having similar dimensions as the cereal, have not been removed from the separator.
The machine is based on the principle that even if the same size the stones are much heavier than the cereal (different specific weight) and for this reason they can be separated thanks to the combination of a net and airflow.
The necessary movement to put the product on the work surface is imprinted through two motion-vibrators.
SCOURER MACHINE (TRIEUR)
DATASHEET DOWNLOAD
The honeycombed cylinder for small kernels (scourer) has an exchangeable case. The honeycomb cylinder allows a separation into two fractions of products with different lengths and sizes.
It consists of a rotating outer shell on which honeycombs have been suitably shaped to achieve maximum efficiency, where the kernels, shorter than the honeycombs diameter, enter.
These shorter kernels, as a result of rotation, are discarded on a vibrating channel that has the task of conveying them in a bag while the "good" product is conveyed, through another vibrating channel, to the downstream process.
Included:
- “good” product bag discharge
- waste discharge
- “good” product discharge to the downstream process
- sampling point
The waste conveying vibrating channel is adjustable (inclination around the cylinder axis) to allow the separation point of the two fractions (“good” and waste product).
Various combinations of single or overlapped cylinders allow to create different job diagrams for any type of requirement.
Here are the main features that distinguish the BioStoneMill honeycombed cylinders
CONSTRUCTION
electro welded steel standard modular that allows assembly in different combinations making any processing diagram possible.
MECHANICS
the bearings are never in contact with the product, the internal organs do not require greasing.
ALVEOLATED DRUMS
made of steel and divided into three elements for an easy replacement, with pocket shaped honeycombs and close axle base and diameters from 1.5 to 20 mm.
MOTORIZATION
gear motor with parallel axis and reaction arm.
SHOVEL ADJUSTMENT
simple and precise with a helical wheel screw conveyor and shovel direct position indication.
DUSTINESS
completely closed construction and designed for a suitable suction system.
NOISINESS
possible isolation with sound absorbing material that allows the compliance with standard rules.
HULLER
Hulling means eliminating the epicarp to ensure maximum cleanliness and avoid serving a product contaminated by external elements and mycotoxins that, if ingested, could result in acute or chronical diseases.
One grindstone “peels” the kernel and prepares it for milling.
The engine controls the grindstone while a fan keeps the waste away (Epicarp).
WHEAT CARYODES
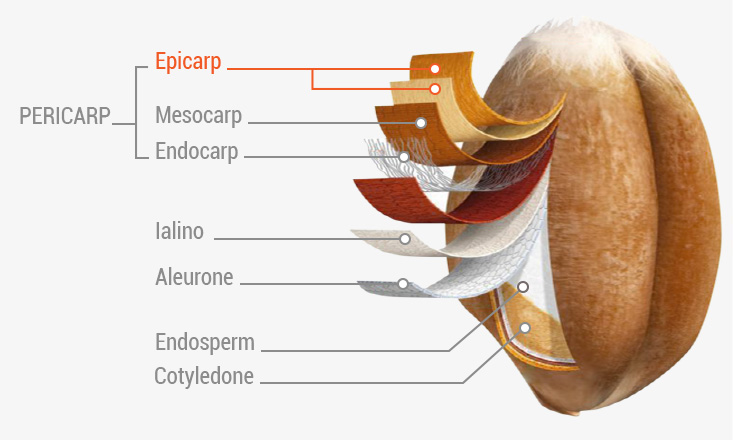
COMPLETE CLEANING UNIT
A solution in only 9 m2, which also guarantees large access for maintenance.
The cleaning unit with the Vibrating Separator and Tarara, Destoner, Scourer Machine and Huller is completed with:
- Receiving hopper
- Magnet
- Dosing screw conveyor
- Elevating screw conveyors
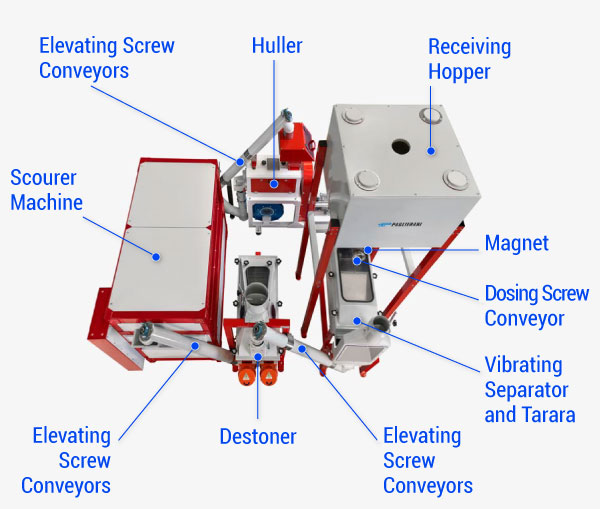
VIBRATING SEPARATOR AND TARARA
DESTONER
SCOURER MACHINE
HULLER
RECEIVING HOPPER
Constructed in carbon steel (304 stainless steel optional).
Complete with level sensors and legs for on-ground installation.
MAGNET
To trap magnetic impurities so they do not contaminate the milled products.
DOSING SCREW CONVEYOR
Screw conveyor for feeding the separator and debranner
ELEVATING SCREW CONVEYORS
Elevating screw conveyors for connections between cleaning machines.
BUCKET ELEVATOR
HEAD
With control gear motor.
FOOT
With product infeed, turnbuckles, openable bottom with shutter for cleaning, and electronic speed control device applied to the driven shaft.
Device measuring the quantity of cereal or legumes, at the entry.
Vibrating separator with tarara: consists of two overlapping vibrating sieves that allow to eliminate the different sized impurities from the cereal.
The upper sieve separates impurities bigger than the cereal, while the lower sieve separates shriveled kernels, soil and all impurities smaller than the cereal.
The choice of the sieve holes opening therefore depends on the size and shape of the cereal being treated.
The sieved cereal passes through the tarara airflow that eliminates shriveled kernels and hay that are lighter than the treated cereal.
In case of processing more than one cereal, it is possible to have more sieves in stock, each of which is suitable for a type of cereal.
The screens are vibrated by two motion-vibrators.
The main purpose of this machine is the stone elimination which, having similar dimensions as the cereal, have not been removed from the separator.
The machine is based on the principle that even if the same size the stones are much heavier than the cereal (different specific weight) and for this reason they can be separated thanks to the combination of a net and airflow.
The necessary movement to put the product on the work surface is imprinted through two motion-vibrators.
DATASHEET DOWNLOAD
The honeycombed cylinder for small kernels (scourer) has an exchangeable case. The honeycomb cylinder allows a separation into two fractions of products with different lengths and sizes.
It consists of a rotating outer shell on which honeycombs have been suitably shaped to achieve maximum efficiency, where the kernels, shorter than the honeycombs diameter, enter.
These shorter kernels, as a result of rotation, are discarded on a vibrating channel that has the task of conveying them in a bag while the “good” product is conveyed, through another vibrating channel, to the downstream process.
Included:
- “good” product bag discharge
- waste discharge
- “good” product discharge to the downstream process
- sampling point
The waste conveying vibrating channel is adjustable (inclination around the cylinder axis) to allow the separation point of the two fractions (“good” and waste product).
Various combinations of single or overlapped cylinders allow to create different job diagrams for any type of requirement.
Here are the main features that distinguish the BioStoneMill honeycombed cylinders
CONSTRUCTION
electro welded steel standard modular that allows assembly in different combinations making any processing diagram possible.
MECHANICS
the bearings are never in contact with the product, the internal organs do not require greasing.
ALVEOLATED DRUMS
made of steel and divided into three elements for an easy replacement, with pocket shaped honeycombs and close axle base and diameters from 1.5 to 20 mm.
MOTORIZATION
gear motor with parallel axis and reaction arm.
SHOVEL ADJUSTMENT
simple and precise with a helical wheel screw conveyor and shovel direct position indication.
DUSTINESS
completely closed construction and designed for a suitable suction system.
NOISINESS
possible isolation with sound absorbing material that allows the compliance with standard rules.
Hulling means eliminating the epicarp to ensure maximum cleanliness and avoid serving a product contaminated by external elements and mycotoxins that, if ingested, could result in acute or chronical diseases.
One grindstone “peels” the kernel and prepares it for milling.
The engine controls the grindstone while a fan keeps the waste away (Epicarp).
WHEAT CARYODES
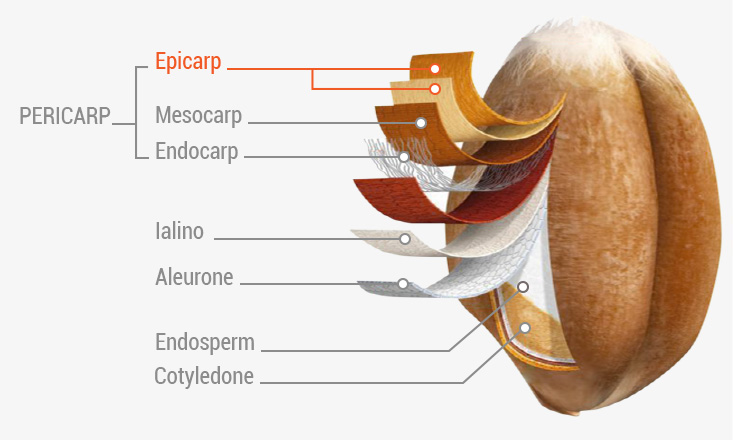
A solution in only 9 m2, which also guarantees large access for maintenance.
The cleaning unit with the Vibrating Separator and Tarara, Destoner, Scourer Machine and Huller is completed with:
- Receiving hopper
- Magnet
- Dosing screw conveyor
- Elevating screw conveyors

VIBRATING SEPARATOR AND TARARA
DESTONER
SCOURER MACHINE
HULLER
RECEIVING HOPPER
LEARN MORE
Constructed in carbon steel (304 stainless steel optional).
Complete with level sensors and legs for on-ground installation.
MAGNET
LEARN MORE
To trap magnetic impurities so they do not contaminate the milled products.
DOSING SCREW CONVEYOR
LEARN MORE
Screw conveyor for feeding the separator and debranner
ELEVATING SCREW CONVEYORS
LEARN MORE
Elevating screw conveyors for connections between cleaning machines.
BUCKET ELEVATOR
LEARN MORE
HEAD
With control gear motor.
FOOT
With product infeed, turnbuckles, openable bottom with shutter for cleaning, and electronic speed control device applied to the driven shaft.